處理污水量按需求定
可售賣地全國
類型廢水處理設備
加工定制是
材質防腐碳鋼
防腐工藝環氧瀝青
電源380v
功率20-40kw
處理量5-1000噸
進水口50mm
出水口110mm
定制加工是
材料碳鋼
材料厚度6mm
處理類型屠宰廢水
排放標準一級A
規格定制
是否定制是
進出水口50
處理水量5-1000噸/每天
進水管徑DN50mm
出水管徑DN1100
生產周期3-5天
電鍍廠廢水處理技術
各電鍍廠的生產工藝,生產規模差別很大,鍍種,廢水濃度均不一致,甚至6—10倍,處理工藝大致可把含鉻廢水和酸洗廢水混合后單獨處理;把含氰廢水和除油廢水混合后單獨處理;其它鍍種廢水混合后單獨處理。廢水水質濃度與處理成本成正比,廢水濃度與采用的生產工藝相關,排放標準與該地的環境容量由當地環境部門確定排放標準,一般分為達標排放GB8978—1996一級和回用水質標準。
工藝流程
含氰廢水→格柵→調節池→廢水 泵→電磁流量計→二級氧化反應池→混合廢水池
Na2SO3H2SO4
含鉻廢水→格柵→調節池→水泵→電磁流量計→還原反應池→混合廢水池
CaOPAM
混合廢水→格柵→混合廢水池→水泵→電磁流量計→中和反應池→壓濾泵→壓濾機→砂濾池→PH調節池→標準化排放口
干污泥經無害集中處置
工藝流程原理簡述
含氰廢水預處理:
含氰廢水經格柵后,進入含氰廢水調節池,經轉子流量計后泵入二級氧化反應池,該池內安裝有PH自動控制儀、ORP自動儀和攪拌機,加藥時可通過和PH和ORP儀反饋的信號而控制加藥量,一級氧化反應是在堿性條件下被氯氧化為氰酸鹽的過程,其反應式分如下兩種步驟:
CN-+ClO-+H2O=CNCl+2OH-(一)
CNCl+2OH-=CNO-+Cl-+H2O(二)
在一級反應過程中,(一)式反應很快,但(二)式反應中PH值小于8.5時,反應速度慢,而且釋放出劇毒物CNCl的危險,因此在級反應過程中污水的PH值要控制到≥11。
第二級氧化反應是將級反應生成的氰酸鹽進一步氧化成N2和CO2,雖然一級反應生成的氰酸鹽毒性很低,僅為氰的1%,但是CNO-易水解成NH3,對環境造成污染,其反應原理為:
2NaCNO+3HOCl=2CO2+N2+2NaCl+HCl+H2O
反應時,該池的PH值應控制在7.5~8之間,因PH≥8時,反應速度慢;當PH太低時,氰酸根會水解成氨,并與次氯酸生成有毒的氯胺。
經二次破氰預處理后,原來的絡合物被打開,廢水直排到混合廢水池后再與混合廢水一并處理。
含鉻廢水預處理:
由于還原反應時,廢水須調PH值至2~3之間,因此將酸洗廢水引進與含鉻廢水混合,可減少酸的用量,降低廢水處理的運行費用,達到以廢治廢的目的。
含鉻廢水經格柵處理后,進入含鉻廢水調節池,經轉子流量計后泵入還原反應池,該池內安裝有PH自動控制儀和ORP儀及攪拌機,PH計與ORP儀可自動控制還原反應池加藥量。電鍍廢水中的六價鉻主要以CrO42-和Cr2O72-兩種形式存在,隨著廢水PH值的不同,兩種形式之間存在著轉換平衡:
2CrO42-+2H+Cr2O72-+H2O
Cr2O72-+2OH-CrO42-+H2O
由上式可以看出在酸性條件下,六價鉻主要以Cr2O72-形式存在,在堿性條件下則以CrO42-形式存在。但是電鍍含鉻廢水、漂洗廢水一般PH都在5以上,多數以CrO42-存在,其還原時通常PH佳控制在2.5~3之間,其反應原理(還原劑以Na2SO3為例)為:
2H2CrO4+3Na2SO3+3H2SO4=Cr(SO4)3+3Na2SO4+5H2O
亞硫酸鈉用量理論上為:亞硫酸鈉∶六價鉻=4∶1,加藥時投料不宜過大,否則浪費藥劑,也可能因生成[Cr2(OH)2SO3]2+而沉淀不下來。
還原后的廢水直排入混合廢水池后再與混合廢水一并處理。
混合廢水處理:
混合廢水為含鉻預處理后廢水、含氰廢水預處理后廢水、鍍鎳、普通鍍銅、除油等廢水,該廢水混合后經格柵處理由防腐泵提升經轉子流量計進入中和反應池,該池內安裝有PH計及攪拌機,當向反應池投加堿(CaO)時,各金屬在一定的PH值下生成相應的氫氧化物沉淀物。根據我們以往所積累的對電鍍廢水行業的處理經驗,混合廢水佳沉淀的PH值為9.5,反應后的出水進入中間水池,再經過經砂濾后,出水的PH還是偏堿性,因此再經PH調節池加酸調節后可達標排放。壓濾后的污泥外運集中深埋或制磚或回收金屬離子或經其它無害化處理
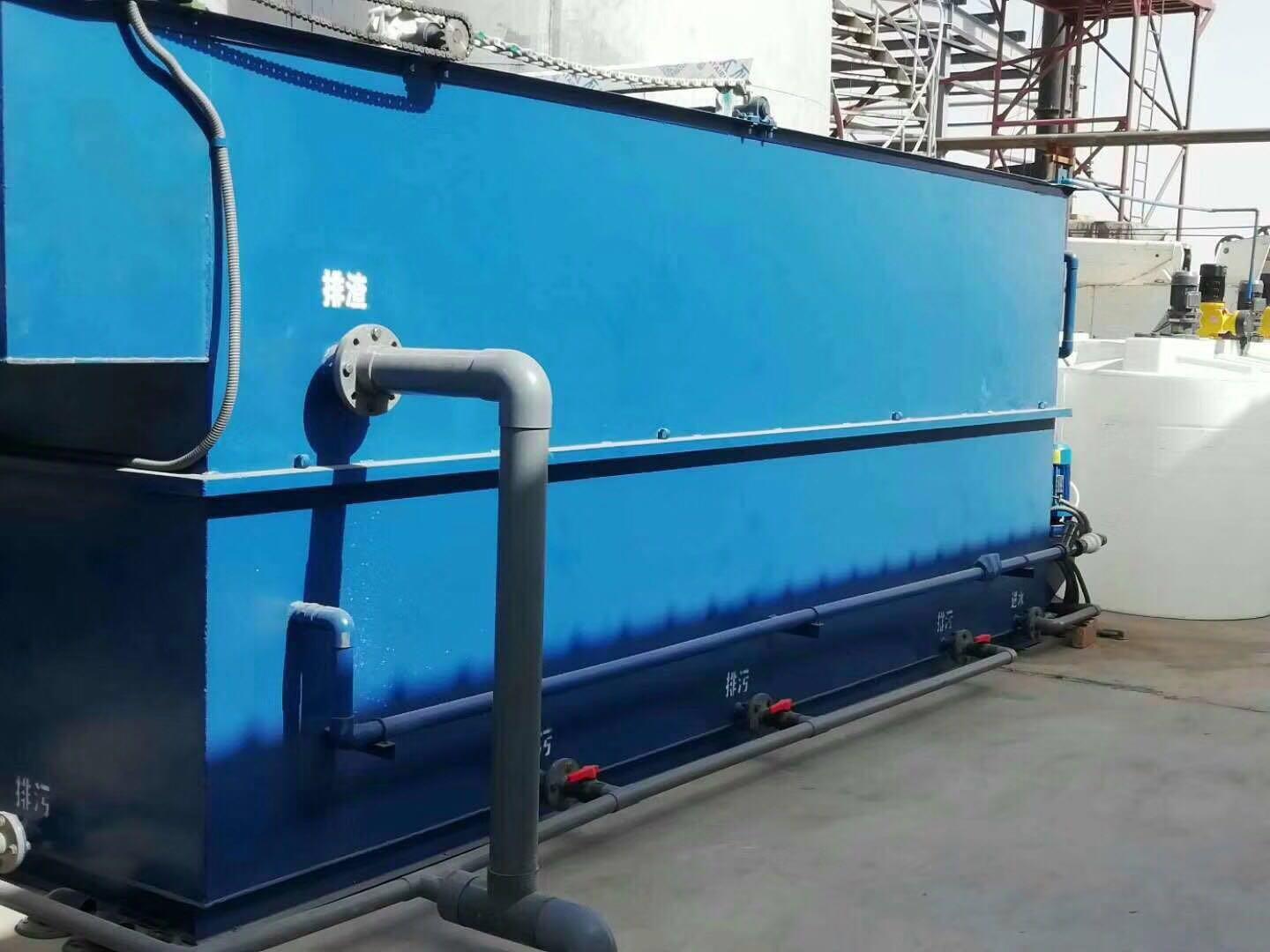
詳情
項目名稱:貴州省貴陽市餐具消毒污水處理工程
治污種類:酒店賓館等使用下來的餐具清洗廢水和消毒廢水
處理規模:日處理量40噸
執行標準:《污水綜合排放標準》(GB8978-1996)中的一級標準要求
處理工藝:采用油水分離預處理+微濾二級處理的處理工藝
項目簡介:餐飲污水處理工程,該工程處理水量為40m³/d,處理效果達到《污水綜合排放標準》(GB8978-1996)中的一級標準要求。
餐具清洗、消毒污水處理特點及難點
餐洗消毒廢水主要是指餐具清洗、消毒時產生的廢水,餐具清洗、消毒污水的特點是水量波動大、瞬時水量大,污水里含有大量的油脂、食物殘渣、消毒劑、表面活性劑等。這種未經 處理的污水進入自然水體后,使水中固體懸浮物、有機物和微生物含量升高,改變水體的物理、化學和生物群落組成,使水質變壞。因此本工程采用油水分離預處理+微濾二級處理的處理工藝。
進水水質及出水水質
根據該市環境監測中心站的污水水質檢驗報告,并參考同類工程的污水水質狀況,確定進水水質如下:
參數(mg/L)
COD
BOD
SS
pH
動植物油
LAS
進水前
≤2000
≤700
≤520
10.00~10.23
300
250
出水后
≤100
≤20
≤70
6~9
10
5.0
解決方案及技術工藝
根據對該餐具消毒廠的實際考察,通過現場調查和資料查找,以及當地市環境監測站監測數據綜合分析,我公司技術組為該餐具消毒廠制定了對應的工藝流程,有效的解決了該餐具消毒廠的清洗、消毒廢水的處理問題。
本工程需要處理的廢水種類有兩類,分別是餐具清洗車間處理的廢水和餐具清洗后消毒出來的廢水,本工程設計規模為100m³/d。根據對污水水質的分析,通過對目前國內外同類污水處理技術的調查研究,結合廠中現有污水收集設施和廠區環境條件,選用油水分離裝置作為初級處理、生膜物微濾作為二級處理的工藝。
處理工藝流程
工藝流程特點
(1)處理方法適應現有大多數餐飲業含油廢水達標排放的處理需要,對現有餐具消毒中心來講,綜合治理速度快,可充分利用廠區的排污管道;
(2)工藝簡單、運行及維護費用低;
(3)保持預處理反應單元對COD、動植物油及洗滌劑的大去除率,提高 污水的可生化性,減少后續好氧反應的能耗;
(4)好氧反應采用生物膜微濾裝置,采用無機膜取代二沉池能實現固液分離,污染物去除效率高,出水水質好;
(5)全部反應裝置可采用地埋式,主體處理設備為碳鋼結構;
結論
本方案實現了餐具消毒洗刷廢水的“減量化、無害化、資源化”,排出的污水經深度處理后達到該市的排放標準要求(《污水綜合排放標準》中的一級標準),運行成本低、出水水質良好,經進一步處理后可達到回用水水質的要求,應用前景較好。污水中CODcr、LAS的含量均較高,可生化性較差,為達到排放要求,處理工藝采取了如下措施:預處理單元在去除CODcr、LAS的同時,明顯提高污水的可生化性;采用生物膜微濾裝置替代傳統的生物接觸氧化+二沉池,經過生物降解和膜分離的共同作用,使水中有害物質含量大大降低;過濾器使生化反應裝置的出水得到進一步的凈化,保證出水水質達到排放標準的要求。
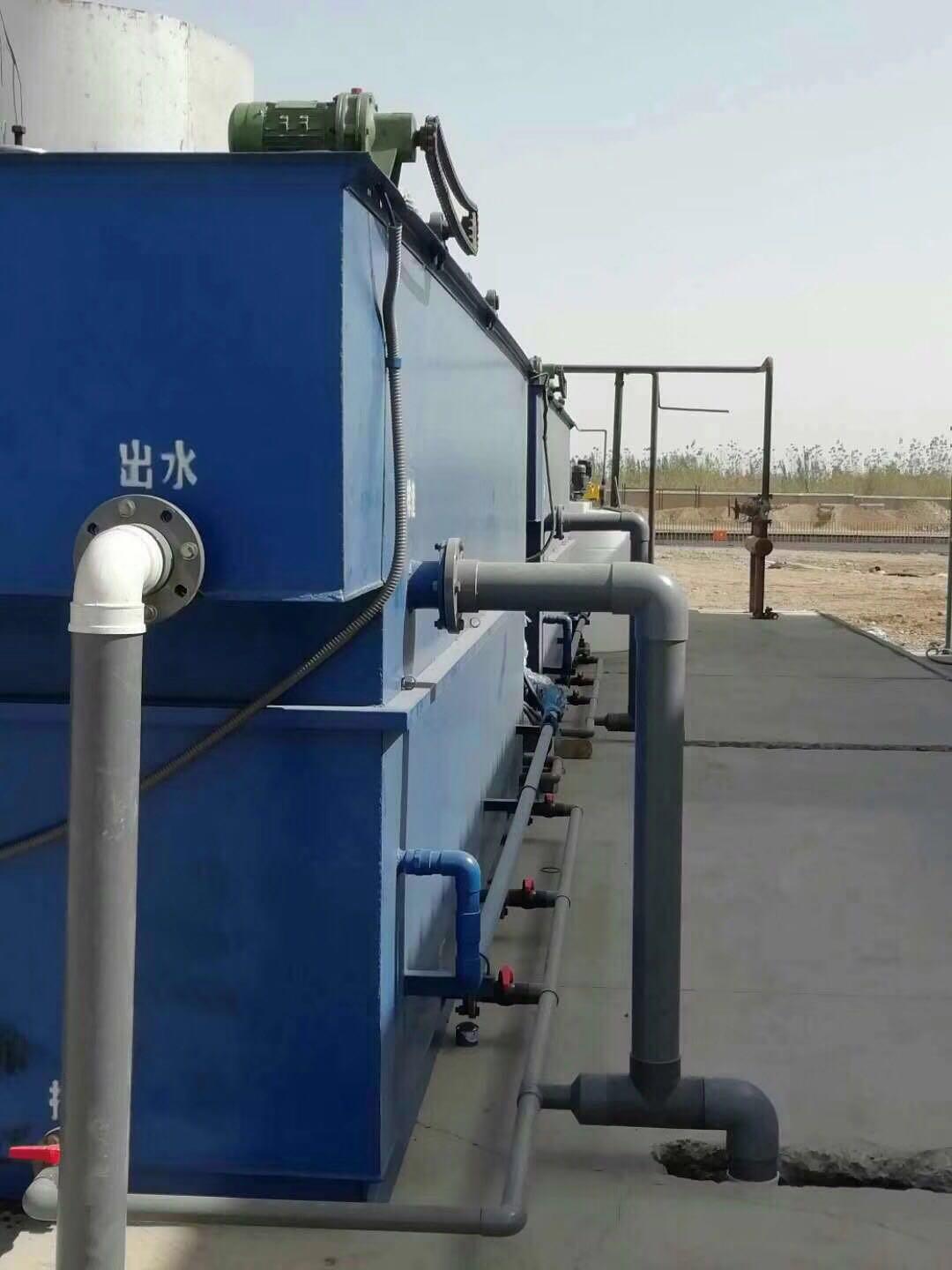
電鍍廢水的來源一般為:(1)鍍件清洗水;(2)廢電鍍液;(3)其他廢水,包括沖刷車間地面,刷洗極板洗水,通風設備冷凝水,以及由于鍍槽滲漏或操作管理不當造成的 “跑、冒、滴、漏”的各種槽液和排水;(4)設備冷卻水,冷卻水在使用過程中除溫度升高以外,未受到污染。電鍍廢水的水質、水量與電鍍生產的工藝條件、生產負荷、操作管理與用水方式等因素有關。電鍍廢水的水質復雜,成分不易控制,其中含有鉻、鎘、鎳、銅、鋅、金、銀等重金屬離子和等,有些屬于致、致畸、致突變的劇毒物質。
廢水來源
電鍍廢水的來源一般為:
(1)鍍件清洗水;
(2)廢電鍍液;
(3)其他廢水,包括沖刷車間地面,刷洗極板洗水,通風設備冷凝水,以及由于鍍槽滲漏或操作管理不當造成的 “跑、冒、滴、漏”的各種槽液和排水;
(4)設備冷卻水,冷卻水在使用過程中除溫度升高以外,未受到污染。
(5)金屬表面處理:金屬表面處理包括表面處理前的清理、電鍍、鈍化膜保護、機械加工及涂料覆蓋等,主要以電鍍為主。
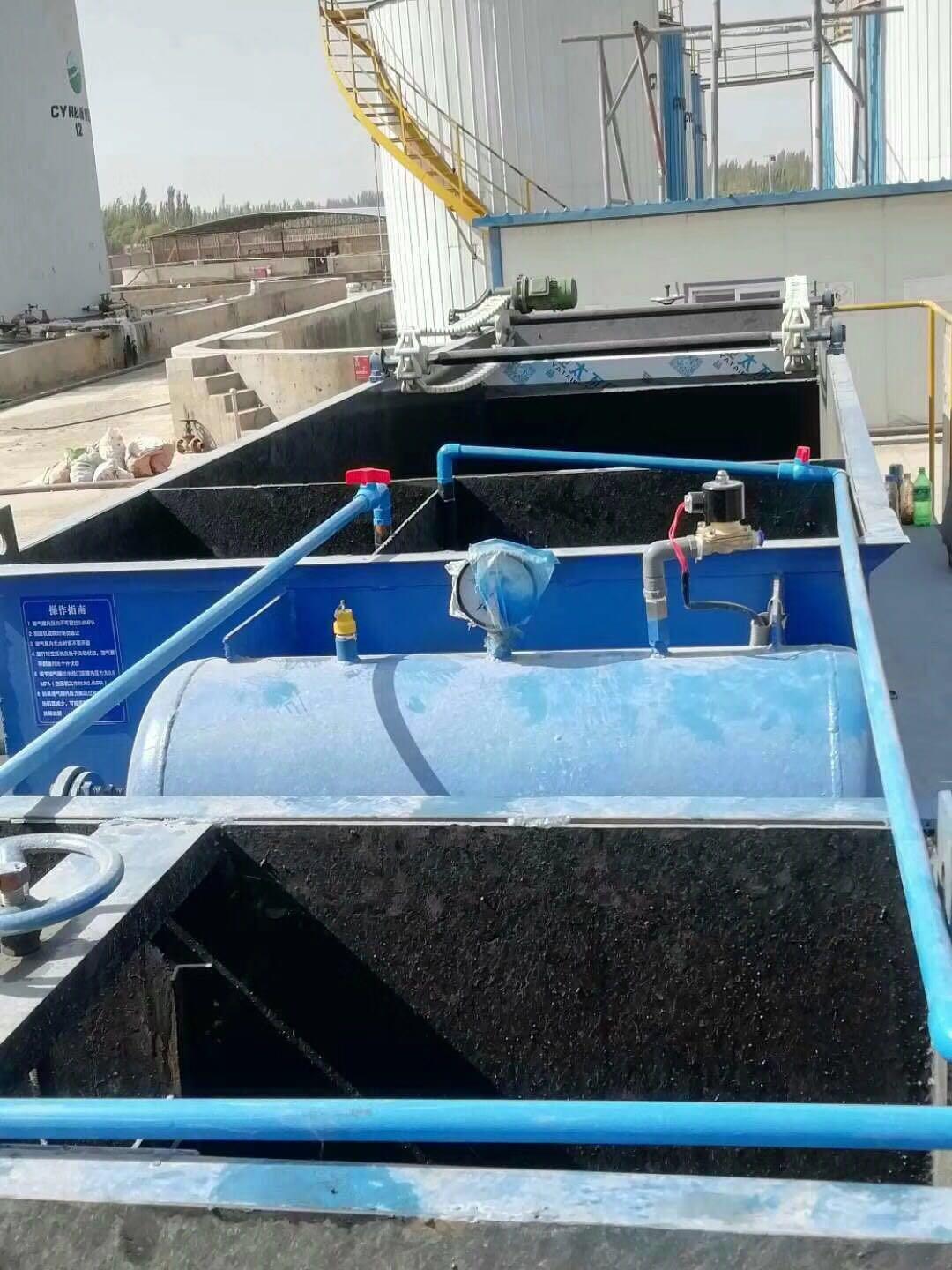
洗煤廢水中含有大量的懸浮物、煤泥和泥砂,故又稱煤泥水,未經處理的煤泥水其懸浮物濃度可以達到5000mg/L以上。由于煤炭本身具有疏水性,洗煤廢水中的一些微小煤粉在水中特別穩定,一些超細煤粉懸浮于水中,靜置幾個月也不會自然沉降。
洗煤廢水是呈弱堿性的膠體體系,主要特點是顆粒表面帶有較強的負電荷,濃度和CODcr濃度都很高;細小顆粒含量高;粘度大;污泥比阻大,過濾性能差。
采用一體化凈水器為主的處理工藝
洗煤廢水處理及精煤回收處理系統選用污水凈化及精煤回收一體化處理設備。洗煤水首先匯入調節池。調節池污水經泵提升,在泵后管道上設置混凝混合器,在混凝混合器前后分別投加助凝劑、混凝劑,然后進入凈化器中,首先經過精煤分選裝置分選出精煤,排出設備,經脫水篩篩分出精煤回收;精煤回收后的廢水經離心分離、重力分離、動態把關過濾及污泥濃縮等過程從凈化器頂部排出經處理后的清水送入清水池,回用或排放,從凈化器底部排出的濃縮煤泥排至煤泥滲濾干化池或用干化設備干化后使用。本所設計的煤泥滲濾干化池使用效果明顯,可以使泥水快速分離,煤泥迅速干化。該工藝針對該類廢水處理成熟可靠、運行穩定,是目前經濟適用的新工藝。
石灰混凝法
石灰-聚丙烯酰胺混凝沉淀法對洗煤廢水具有較好的處理效果,但石灰的投加方式、聚丙烯酰胺的性質以及投藥順序對處理效果都有一定程度的影響,尤其是投藥順序與傳統投加順序不同。
濕投石灰時,石灰溶液的濃度對處理效果有影響。當石灰投加量一定時,濃度越低,沉速越快,合液的清水分離率越高,但從洗煤廢水中實際分離出的清水量卻隨著石灰溶液濃度的降低而略有減少。沉速隨石灰溶液濃度的降低而提高,主要是因為石灰溶液濃度的降低,導致了加藥后混合液體積的增加,從而使混合液中33濃度降低,同時對煤泥起到了水力淘洗的作用,使粘度下降,因此,沉速有所提高。先投聚丙烯酰胺后投石灰效果好,不僅沉速快,而且清水分離率也高。另外,從絮凝體的外觀來看,先投聚丙烯酰胺生成的顆粒粒度大,強度也高,有利于進一步脫水。加藥后ph值的變化對聚丙烯酰胺的絮凝性能有較大影響。一般來說,聚丙烯酰胺在ph值很寬的范圍內效能都很高,但隨著56值的變化,聚丙烯酰胺的作用也發生很大變化。
電石渣和PAM
礦洗煤廢水是一個膠體分散體系,并且膠粒表面帶有較強的負電荷,所以,在處理這類洗煤廢水時,需要向廢水中投加混凝劑,降低電位,破壞膠體的穩定性,從而達到泥水分離的目的。石灰和電石渣的處理效果為佳,但形成的顆粒粒徑較小,沉降速度緩慢,且凝聚體的過濾性能差,難于進一步脫水,需投加絮凝劑。由于石灰和電石渣的化學成分基本一樣,而電石渣是工業廢渣,電石渣能破壞洗煤廢水的穩定性.使煤泥顆粒凝聚沉降,但沉降速度比較緩慢,應投加絮凝劑,提高沉降速度,改善沉淀性能。通過試驗.并考慮經濟因素,選非離子型PAM作為絮凝劑,考慮到電石渣與PAM的加入量以及加藥后的攪拌時間對沉速都有影響。影響沉降效果的*主要因素是PAM的投加量,其次是電石渣的投加量。
http://m.pyxymg.com